What is Silica Fume?
Silica fume, also known as microsilica or condensed silica fume, is an ultrafine powder collected as a by-product of silicon and ferrosilicon alloy production. This amorphous form of silicon dioxide consists of spherical particles with an average diameter of 150 nanometers, making it approximately 100 times finer than average cement particles. Unlike naturally occurring minerals, silica fume is an engineered material that emerges from the reduction of high-purity quartz with coal in electric arc furnaces during the production of silicon metals and alloys.
The formation process involves the oxidation of silicon dioxide vapor at high temperatures, which condenses into tiny spherical particles of amorphous silica. This industrial origin distinguishes silica fume from natural pozzolanic materials and contributes to its unique properties and applications. The material contains more than 90% silicon dioxide, with trace amounts of other elements depending on the source of production.
The historical development of silica fume as a valuable construction material began in the 1970s when environmental regulations required silicon metal producers to capture and filter the material rather than release it into the atmosphere. This regulatory requirement led to the discovery of silica fume’s beneficial properties in concrete applications, transforming what was once considered an industrial waste product into a highly sought-after material.
Uses of Silica Fume
Construction Industry
The primary application of silica fume lies in high-performance concrete production, where it serves as a supplementary cementitious material. When added to concrete mixtures, silica fume significantly enhances both mechanical properties and durability. Its ultrafine particles fill the microscopic spaces between cement particles, creating a denser concrete matrix that exhibits:
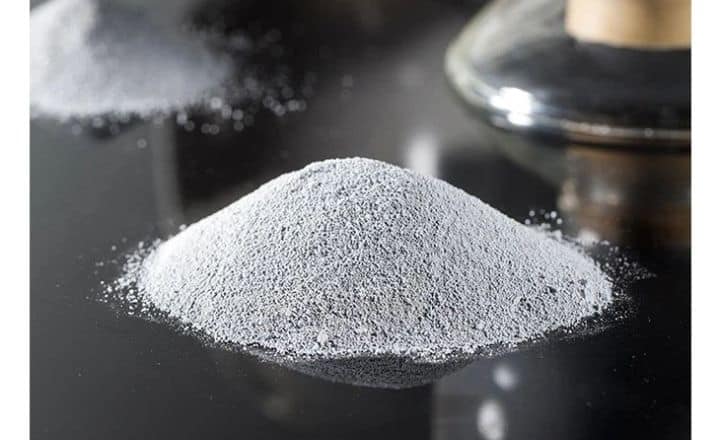
- Increased compressive strength, often reaching values above 100 MPa
- Enhanced durability against chemical attack from aggressive environments
- Reduced permeability, limiting the ingress of harmful substances
- Improved resistance to freeze-thaw damage in cold climates
- Better protection against reinforcement corrosion
- Superior bond strength between concrete and reinforcement
- Increased abrasion resistance in industrial floors and pavements
The material’s ability to produce high-strength concrete has revolutionized the construction of high-rise buildings, bridges, and marine structures, enabling more slender designs and longer spans while maintaining structural integrity.
Industrial Applications
Beyond construction, silica fume finds applications in various industrial sectors:
- Refractory materials production for high-temperature applications
- High-performance grouts and mortars for specialized repairs
- Oil well cementing for deep-water operations
- Marine structure protection in aggressive environments
- Bridge deck overlays for extended service life
- Parking structure rehabilitation and protection
- Nuclear waste containment structures
- Underground mining support systems
- Tunnel linings and repairs
The versatility of silica fume in these applications stems from its ability to enhance both strength and durability characteristics of cementitious materials, making it particularly valuable in challenging environmental conditions.
Properties of Silica Fume
Physical Characteristics
Silica fume possesses several distinctive physical properties that contribute to its effectiveness:
- Particle size: 0.1-0.3 micrometers average diameter
- Specific surface area: 15,000-30,000 m²/kg
- Bulk density: 200-300 kg/m³
- Spherical particle shape
- Non-crystalline structure
- Color ranging from light to dark gray
- Low bulk density in its original state
- High packing density when properly dispersed
These characteristics, particularly its extreme fineness and high specific surface area, enable silica fume to function effectively as a pozzolanic material and micro-filler in cementitious systems. The spherical shape of particles contributes to improved workability in fresh concrete when properly dispersed.
Chemical Properties
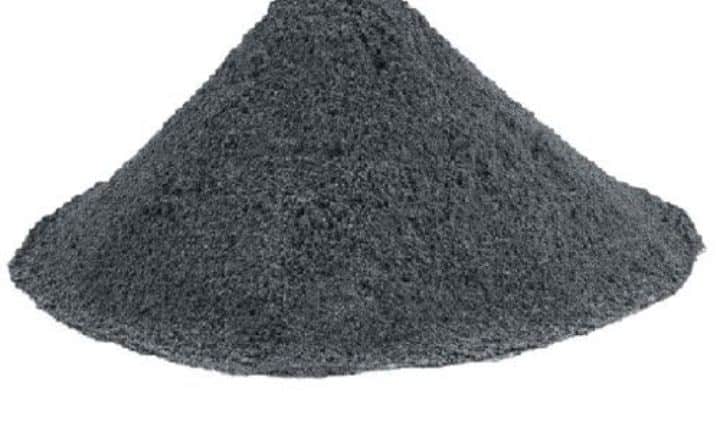
The chemical composition of silica fume typically includes:
- Silicon dioxide (SiO₂): 85-98%
- Carbon: 0.5-2%
- Iron oxide: 0.2-0.8%
- Alkalis: 0.5-2%
- Calcium oxide: 0.1-0.5%
- Magnesium oxide: 0.2-1.5%
- Sulfur trioxide: 0.2-0.4%
The high amorphous silica content enables strong pozzolanic reactions with calcium hydroxide produced during cement hydration, forming additional calcium silicate hydrate (C-S-H) gel that strengthens the concrete matrix. This reaction not only increases strength but also reduces the potential for alkali-silica reaction and improves chemical resistance.
Silica Fume Production
Unlike traditional mining operations, silica fume is collected as a by-product of silicon metal and ferrosilicon alloy production. The production process involves several sophisticated steps:
- Raw Material Preparation
- Selection of high-purity quartz
- Preparation of carbon sources (coal, coke, woodchips)
- Quality control of input materials
- Smelting Process
- Electric arc furnace operation at temperatures exceeding 2000°C
- Reduction of quartz to produce silicon metal
- Generation of silicon dioxide vapor
- Collection System
- Cooling and condensation of the vapor
- Filtration through baghouse systems
- Monitoring and control of particle size distribution
- Processing and Quality Control
- Testing for chemical composition
- Verification of physical properties
- Certification for construction use
- Storage and Distribution
- Packaging in bags or bulk containers
- Storage in controlled environments
- Transportation logistics
Modern production facilities employ sophisticated collection systems to ensure high-quality material while maintaining environmental standards. The efficiency of collection systems has improved significantly over the years, reducing atmospheric emissions while increasing the recovery of this valuable material.
Environmental Impact
Benefits
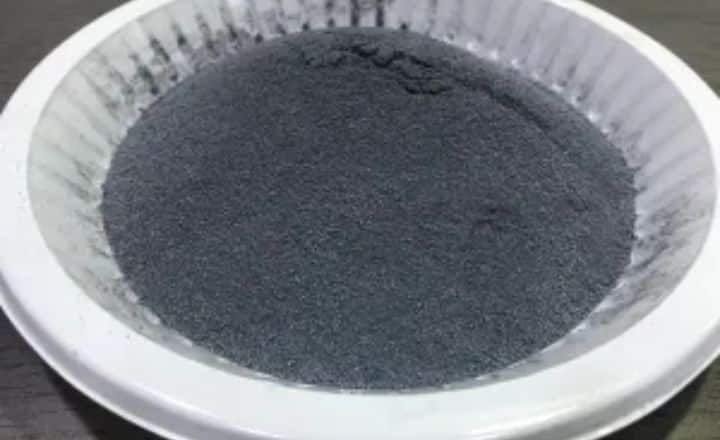
The utilization of silica fume presents several environmental advantages:
- Reduces cement consumption in concrete production by 5-15%
- Decreases CO₂ emissions associated with cement manufacturing
- Utilizes an industrial by-product that would otherwise require disposal
- Extends the service life of concrete structures, reducing maintenance and replacement needs
- Contributes to sustainable construction practices
- Enables the design of more efficient structures using less material
- Reduces the carbon footprint of construction projects
Challenges
While silica fume production itself is a by-product recovery process, some environmental considerations include:
- Energy consumption in collection and processing
- Transportation-related emissions
- Dust control during handling and application
- Workplace safety requirements due to the material’s fine nature
- Need for specialized handling equipment and procedures
- Potential health risks if proper safety measures are not followed
- Higher initial cost compared to conventional concrete materials
Conclusion
Silica fume represents a remarkable example of how industrial by-products can be transformed into valuable construction materials that enhance building performance and sustainability. Its continued use and development in construction and industrial applications demonstrate the potential for innovative materials to address both technical and environmental challenges in modern construction.
The future of silica fume looks promising as construction industry demands for high-performance materials continue to grow. Research continues to explore new applications and optimize its use in various contexts. As sustainability becomes increasingly important in construction, the role of silica fume as an environmentally friendly supplementary cementitious material is likely to expand further.
The success of silica fume illustrates the potential for industrial ecology, where waste products from one process become valuable inputs for another, contributing to more sustainable industrial practices. As construction technology advances, the importance of such materials in creating more durable, sustainable, and resilient infrastructure will only increase. The ongoing development of new applications and improved understanding of its behavior in various environments suggests that silica fume will continue to play a crucial role in the future of construction technology and sustainable development.